STILRIDE begins a collaboration with French-Swedish ADAXIS. The goal is to further develop and fine-tune the software that STILRIDE uses when they bend and fold sheet steel in an origami-like process. Through the collaboration, more parts can be manufactured locally, which is a big step towards the goal of local micro-factories.
The entire life cycle of STILRIDE’s first motorcycle SUS1 is intended to be as durable as possible. An important step in this is the manufacturing itself, where STILRIDE aims for local production. The idea of micro-factories, where each individual motorcycle is built locally in the relevant market, has therefore been there from the beginning.
One of the great advantages of our manufacturing technology is that it is based on sheet steel that we fold and bend. This not only means that we save on materials, but also that the transport of the raw material becomes extremely efficient compared to the finished product. Through local micro-factories, we can take full advantage of this all the way to the country where the product is sold and used.
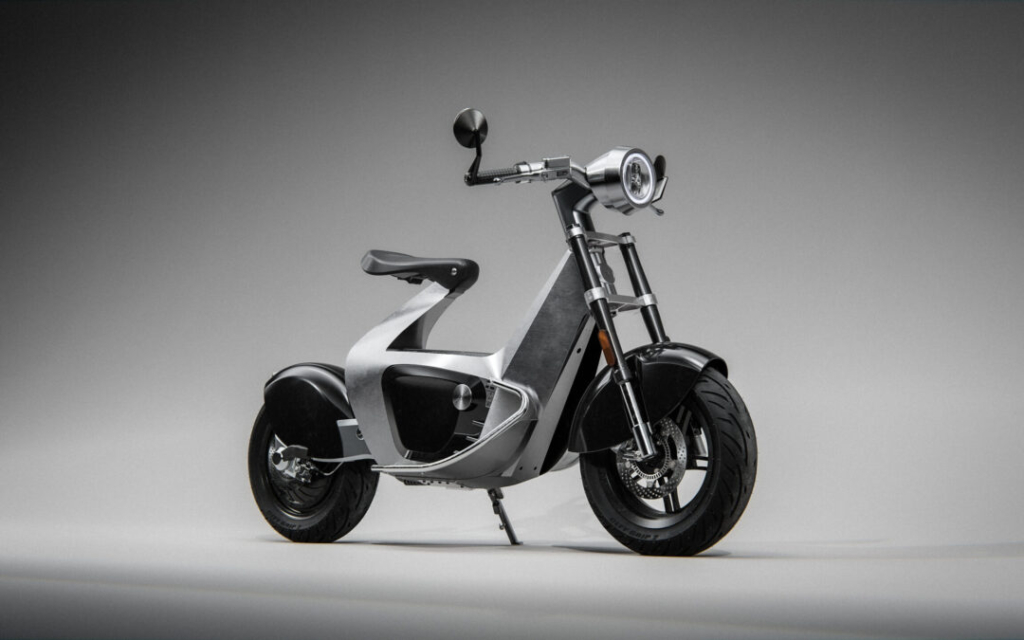
The key to being able to produce the entire chassis locally is a simplified and automated process where a robot guarantees equal results every time. The collaboration with ADAXIS adds another dimension to this, as the company specializes in simplifying robot control, but also makes it possible, through 3D printing, to create additional parts for the motorcycle through the robot used.
Through ADAXIS, it will now also be possible to print new parts in the microfactories, parts that would otherwise have had to be brought in from another manufacturer. More specifically, in the first stage, it is about covers, screens and a number of brackets that can now be easily built on site according to the same principle that STILRIDE offers in general.
With robotization, we can push the limits of what can be manufactured using 3D technology, both in terms of size and shape. The challenge is that programming robots for 3D is often advanced and elusive. Our goal is to speed up the process and make it more intuitive, even when it comes to really complex projects, so that everyone can benefit from this technology, says Emil Johansson, co-founder of ADAXIS.
ADAXIS has knowledge and experience that will further simplify and improve the process and at the same time guarantee that the end result will be the same regardless of where in the world the final production takes place. This has the potential not only to save significantly on the environmental footprint, but also to create a lot of jobs locally.
The collaboration between STILRIDE and ADAXIS also gives the opportunity to quickly set up a micro-factory in France in the long term, but the first one will be opened shortly in Nacka strand, next to STILRIDE’s headquarters.
The first factory is expected to be up and running in the spring, and there we can also start to put the last details before a series production of SUS1. The advantages of the micro-factory idea are many, not least from the aspect that we will always be able to produce on-demand and also be able to scale up and down faster in relation to how much is ordered.